What Machines Are Used to Make Tempered Glass?
01 September 2024
Tempered glass is a type of safety glass known for its strength and thermal resistance. It's widely used in automotive, architectural, and household applications. But what machines are essential in the process of making tempered glass? This article explores the key equipment used in glass tempering, including various glass tempering furnaces, bending machines, and post-production processing equipment, focusing on aspects like heat control and temperature management.
1. Glass Tempering Furnace
The heart of the tempered glass production process is the glass tempering furnace. This machine heats flat or bent glass to a high temperature (typically around 620-650°C) before rapidly cooling it with high-pressure air blasts. This heating and cooling process creates compressive stress on the glass surface and tensile stress inside, making it four to five times stronger than untreated glass.
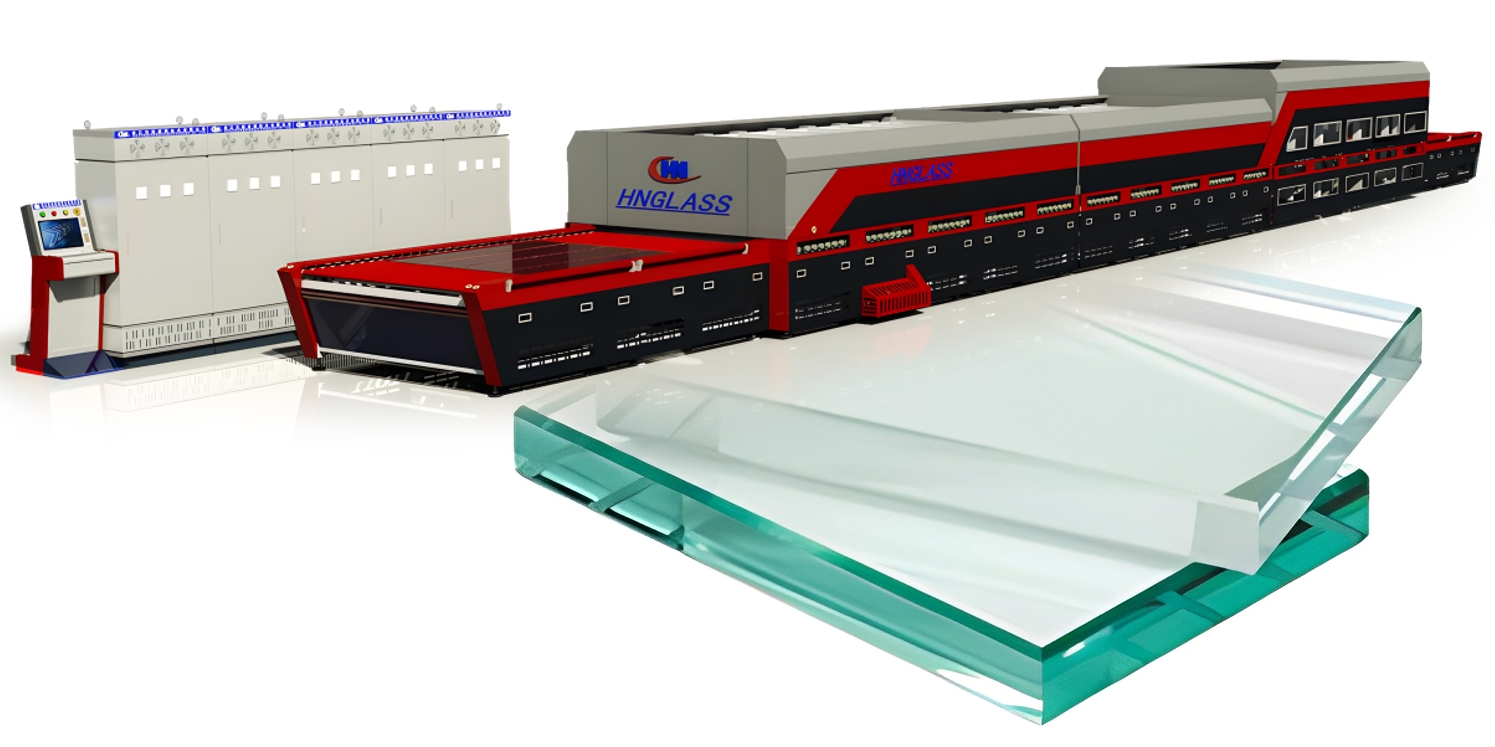
Key Types of Glass Tempering Furnaces:
- Flat Glass Tempering Furnace: Used primarily for standard flat glass tempering, this furnace is crucial in the production of windows, tabletops, and other flat glass products. This furnace type is optimized for consistent heat control and uniform cooling to ensure high-quality results.
- Bent Glass Tempering Furnace: This specialized furnace is used for producing bent tempered glass, commonly found in automotive windshields and curved architectural applications. The furnace integrates the bending and tempering process in a single operation. Glass is heated to a softening point, bent into the desired shape using molds or gravity, and then rapidly cooled to achieve the required strength.
- Convection Glass Tempering Furnace: This advanced type of furnace uses convection heating for more precise and efficient heat distribution. It’s especially beneficial for low-emissivity (Low-E) coated glass, which requires uniform temperature control to maintain coating integrity during tempering.
Integrated Systems:
- Heat Control Systems: Integrated into the tempering furnaces, these systems manage the exact temperature profile required for different glass types and thicknesses. Maintaining a uniform temperature throughout the heating zone is essential for achieving consistent tempering quality.
- Temperature Control Systems: These systems ensure that the glass is cooled at the correct rate, which is critical to prevent thermal stress. Advanced temperature sensors and feedback loops maintain optimal cooling conditions.
2. Glass Bending Tempering Machines
Glass bending tempering machines refer to a broader range of equipment that includes the bending and tempering of glass as separate or combined processes. These machines often involve bending glass first using dedicated bending furnaces or bending systems before transferring it to the tempering stage. The difference lies in the separation of processes, where the glass bending and tempering may not be as integrated as in a bent glass tempering furnace.
Difference Between Bent Glass Tempering Furnace and Glass Bending Tempering Machines:
- Bent Glass Tempering Furnace is highly integrated, performing both bending and tempering within a single furnace, which streamlines the production of curved tempered glass.
- In contrast, Glass Bending Tempering Machines may involve distinct stages, often using separate bending and tempering equipment, allowing for flexibility in handling complex or specialized glass shapes.
3. Pre-Processing Equipment
Before glass is tempered, it undergoes various preparation stages. Pre-processing equipment includes glass cutting machines, edge grinding machines, and washing units that prepare the glass for tempering. Proper preparation is crucial as any imperfections can cause the glass to break during the tempering process.
4. Post-Production Processing Equipment
After tempering, the glass often requires additional processing to meet specific requirements. This stage includes:
- Glass Cutting Machines: Even though cutting is typically done before tempering, in some cases, small adjustments or edge trimming may be necessary post-tempering. Special water jet or laser cutting machines are used that minimize stress and avoid shattering.
- Edge Grinding and Polishing Machines: After tempering, edges of the glass are sometimes smoothed using grinding and polishing machines. This step improves safety by removing sharp edges and enhances the glass's appearance.
- Drilling Machines: For applications requiring holes, such as in shower doors or architectural fittings, drilling machines with specialized bits for tempered glass are used. These machines are designed to work without causing cracks or compromising the integrity of the tempered glass.
- Inspection and Quality Control Systems: Automated inspection machines scan the tempered glass for any defects such as scratches, bubbles, or inconsistencies in the tempering process. These systems ensure that the glass meets the high-quality standards required for safety applications.
Conclusion
The production of tempered glass relies heavily on specialized machines like glass tempering furnaces, glass bending tempering machines, pre-processing, and post-production equipment. Each piece of machinery plays a critical role in ensuring the glass meets required safety and quality standards. From initial shaping and tempering to final adjustments and inspections, the complex interplay of these machines highlights the technical expertise and precision needed to produce high-quality tempered glass. As a leading manufacturer of glass tempering furnaces, we are more than happy to provide you with personalized advice. Feel free to send your inquiries to [email protected] at your convenience.