The process of making glass involves various stages, each requiring specialized machines that perform specific tasks to produce different types of glass, including flat glass and insulated glass. Here, we’ll dive deeper into each machine used in glass production, with a special focus on the glass tempering furnace, its types, and how it plays a crucial role in the process.
1. Glass Melting Furnace
The glass-making process starts with the glass melting furnace, where raw materials such as sand, soda ash, limestone, and other additives are melted. These furnaces operate at extremely high temperatures (up to 1700°C) to convert the solid materials into molten glass.
Types of Glass Melting Furnaces:
- Regenerative furnaces: Use a heat recovery system to improve energy efficiency.
- Electric furnaces: Utilize electricity to generate heat and are often used in small-scale or specialized glass manufacturing.
- Oxygen-fired furnaces: Reduce emissions by burning oxygen instead of air.
These furnaces are typically lined with heat-resistant materials to withstand the high temperatures and maintain energy efficiency.
2. Glass Forming Machine
After the molten glass is prepared, it must be shaped into its final form. This is where the glass forming machine comes in. Depending on the type of glass being produced, various forming methods are used:
- Float glass process: This method is widely used for producing flat glass. Molten glass is floated on a bed of molten tin, which ensures that the glass remains perfectly flat while cooling.
- Press and blow forming: Commonly used for bottles and containers, where molten glass is pressed and blown into a mold.
- Rolling forming: This process is used for patterned or textured glass, where molten glass is passed between two rollers that shape it.
3. Glass Tempering Furnace
The glass tempering furnace plays a crucial role in producing tempered glass, known for its strength and safety properties. The tempering process involves heating the glass to around 620°C and then rapidly cooling it with high-pressure air. This creates compressive stress on the outer surface and tensile stress inside, resulting in glass that is much stronger and safer than annealed glass.
Types of Glass Tempering Furnaces:
- Horizontal Tempering Furnace: This is the most common type of tempering furnace. Glass sheets are placed horizontally on rollers and transported through a heating chamber. After reaching the desired temperature, they are cooled rapidly using high-pressure air. Horizontal furnaces are ideal for flat glass.
- Vertical Tempering Furnace: In a vertical tempering furnace, the glass sheets are suspended vertically and moved through the furnace on rollers. This method reduces the risk of deformation that can occur in horizontal furnaces, especially for thinner or more delicate glass. It’s an ideal option for architectural glass and specialty applications where surface quality is critical, as it avoids roller marks or distortions. This furnace type is commonly used for producing high-quality flat glass and insulating glass.
- Convection Tempering Furnace: Convection tempering furnaces utilize forced hot air to heat the glass uniformly. This technique is especially effective for glass with coatings, like low-E (low emissivity) glass, which can be challenging to heat evenly using traditional methods. The convection process ensures that the heat reaches every part of the glass evenly, resulting in fewer defects and a better-quality finish. These furnaces are suitable for tempering glass used in energy-efficient windows and facades.
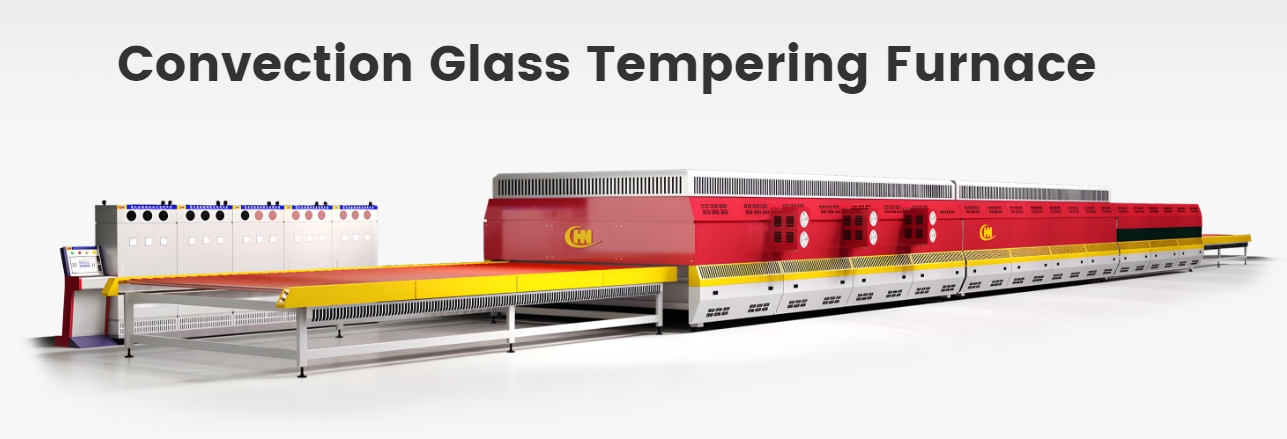
- Continuous Tempering Furnace: This type of furnace is designed for large-scale production, where a continuous supply of glass enters at one end, passes through the heating and cooling zones, and exits fully tempered at the other end. Continuous tempering furnaces are highly efficient and are used in high-output operations such as producing glass for automotive windshields, large building facades, or flat panel displays. These systems are fully automated and optimized for fast processing, making them ideal for industries requiring high volumes of tempered glass.
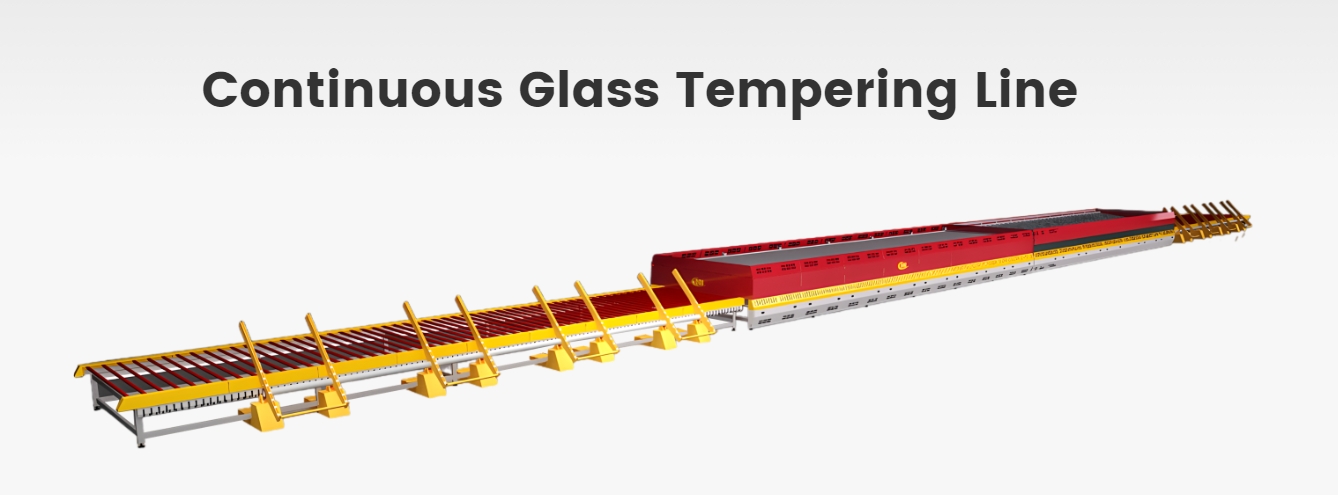
- Cooling System: The cooling blower in a glass tempering furnace is critical. It rapidly cools the glass to create the surface compression that gives tempered glass its strength. Some tempering furnaces allow customization of the cooling process based on the thickness and type of glass.
Tempered glass is used in a variety of applications including windows, doors, automotive glass, and even in electronic devices due to its ability to break into small, harmless fragments when shattered.
4. Glass Laminating Machine
For creating laminated glass, a glass laminating machine bonds multiple layers of glass with an interlayer, often polyvinyl butyral (PVB). The process involves heating and pressing the layers together under vacuum conditions. This creates laminated glass, which is valued for its safety properties. If broken, the interlayer keeps the glass shards together, reducing the risk of injury.
Types of Glass Laminating Machines:
- Autoclave Laminating Machine: After bonding the layers, the glass is placed in an autoclave where it is subjected to high pressure and heat to ensure proper adhesion.
- Vacuum Laminating Machine: The glass and interlayer are laminated in a vacuum environment, eliminating air bubbles that could affect clarity.
5. Glass Processing Machines
Glass processing machines handle various secondary tasks such as cutting, grinding, drilling, and polishing. These machines are crucial for giving glass the necessary dimensions, shapes, and edge finishes needed for installation.
- Cutting Machines: Use water jets or diamond blades to cut glass with precision.
- Drilling Machines: Specifically designed to create holes in glass, commonly used in architectural applications.
- Edging Machines: These machines finish the edges of glass to ensure smoothness and remove sharpness, which is especially important for safety glass.
6. Insulated Glass Production Machinery
Insulated glass (IG) units, or double-glazed glass, are used for thermal insulation in buildings. Insulated glass production machinery assembles two or more panes of glass, with a space between them filled with air or gas (such as argon) to improve insulation properties.
- Desiccant Filling Machines: Fill the spacer bars with desiccants to prevent condensation inside the IG unit.
- Sealing Machines: Seal the edges of the IG unit to ensure airtightness, using materials such as butyl or polysulfide.
- Gas Filling Machines: Introduce insulating gases like argon or krypton into the space between the panes for better thermal performance.
Conclusion
From the initial melting of raw materials to the final processing stages, each machine involved in glass production is crucial to the quality of the finished product. The glass melting furnace begins the process by creating molten glass, which is then shaped in the glass forming machine. For enhanced strength, glass passes through a glass tempering furnace, while glass laminating machines bond layers for added safety. Lastly, glass processing machines ensure precision, and insulated glass production machinery provides energy-efficient solutions. Understanding these machines helps you appreciate the complexity and precision involved in making glass products for various industries.